

That is, to change the pressure angle and pitch of the worm without changing the pitch line parallel to the axis, in accordance with the relationships shown in Equations 9-4: Usually, the crowning is done to the worm gear, but in this method the modification is on the worm. This is a very complex method, both theoretically and practically. Use A Worm With A Larger Pressure Angle Than The Worm Gear. The hob axis is shifted slightly left and then right, Δθ, in a plane parallel to the worm gear axis, to cut a crown effect on the worm gear tooth. In standard cutting, the hob axis is oriented at the proper angle to the worm gear axis. This results in a crowning effect, shown in Figure 9-7. Then the worm gear is finished with the same hob by recutting with the hob axis shifted parallel to the worm gear axis by ±Δ h. The first step is to cut the worm gear at standard center distance. Recut With Hob Center Distance Adjustment. This creates teeth contact in the center region with space for oil film formation.Ģ. Whose pitch diameter is slightly larger than that of the worm. However, it is relatively easy to obtain a crowned worm gear by cutting it with a hob Proper tooth contact and a complete oil film are usually not possible. This crownless worm gear is very difficult to assembleĬorrectly. Cut Worm Gear With A Hob Cutter Of Greater Pitch Diameter Than The Worm.Ī crownless worm gear results when it is made by using a hob that has an identical There are four methods of crowning wormġ. This can favorably impact enduranceĪnd transmission efficiency of the worm mesh. Not only can it eliminateĪbnormal tooth contact due to incorrect assembly, but it also provides for the forming of an oilįilm, which enhances the lubrication effect of the mesh. Standard values of radial module, m t, are presented in Table 9-1.įigure 9-6 9.3 Crowning Of The Worm Gear ToothĬrowning is critically important to worm gears (worm wheels). A special worm hob is required to cut a Type III worm gear. Per JIS, Type III worm uses a radial module m t and cutter pressure angle α c = 20° as the module and pressure angle. In this type, the normal pressure angle α n has the tendency to become smaller than that of the cutter, α c. It is an involute helicoid, and is known by that name.
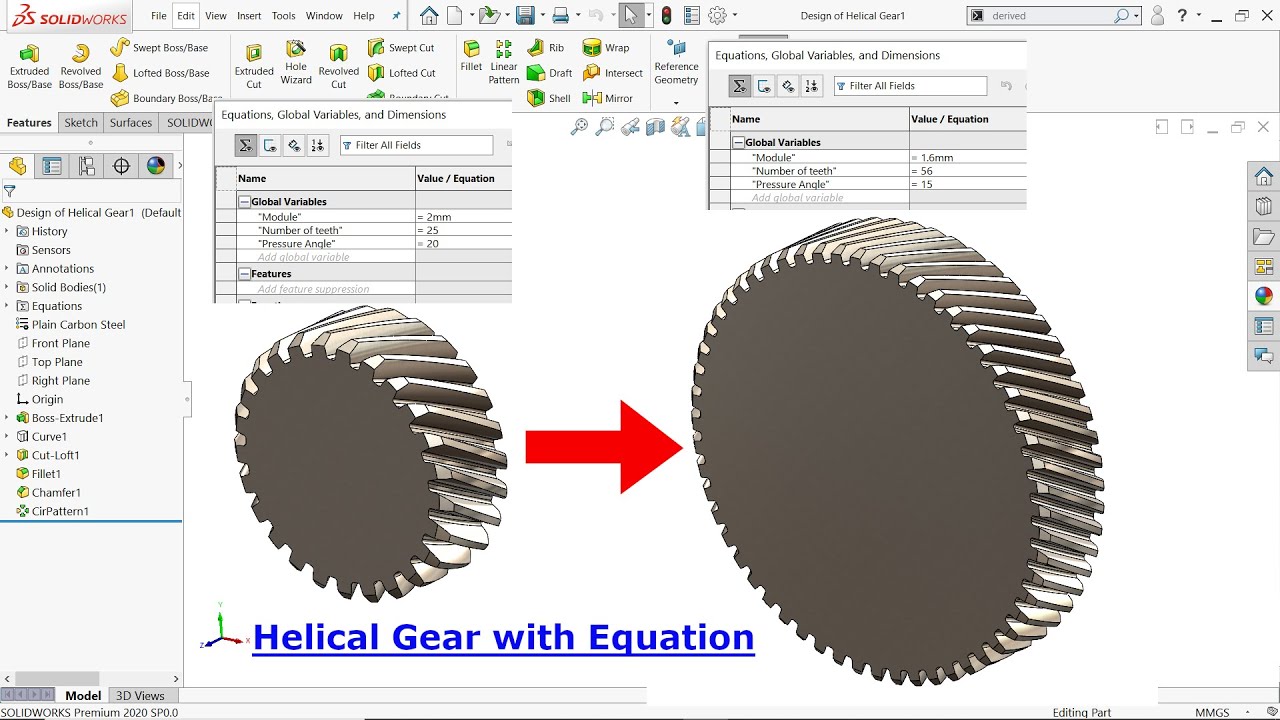
Type IV Worm: This tooth profile is involute as viewed from the radial surface or at the lead angle. Type III Worm: This worm is formed by a cutter in which the tooth profile is trapezoid form viewed from the radial surface or axial plane set at the lead angle. Type II Worm: This tooth profile is trapezoid viewed in the normal surface. Type I Worm: This worm tooth profile is trapezoid in the radial or axial plane. There are four worm tooth profiles in JIS B 1723, as defined below. Referring to Figure 9-4, for a lead angle ɣ, measured on the pitch cylinder, each rotation of the worm makes the thread advance one lead.

Thus, a one-thread worm is equivalent to a one-tooth gear and two-threads equivalent to To the number of teeth in a gear of a screw type gear mesh. The number of threads in the worm is equivalent Generally, the mesh has a 90° shaft angle. Thus, a worm is characterized by theĩ.1.3 Pitch Diameters, Lead and Lead AngleĬylindrical worms may be considered cylindrical type gears with screw threads. For slightly smallerĪngles, there can be two, three or even more threads. The worm can be considered resembling a helical gear with a high helix angle.įor extremely high helix angles, there is one continuous tooth or thread. A high pressure angle is favored and in some applications values as high as 25° and 30° are used. The standard values apply to the central section of the mesh.
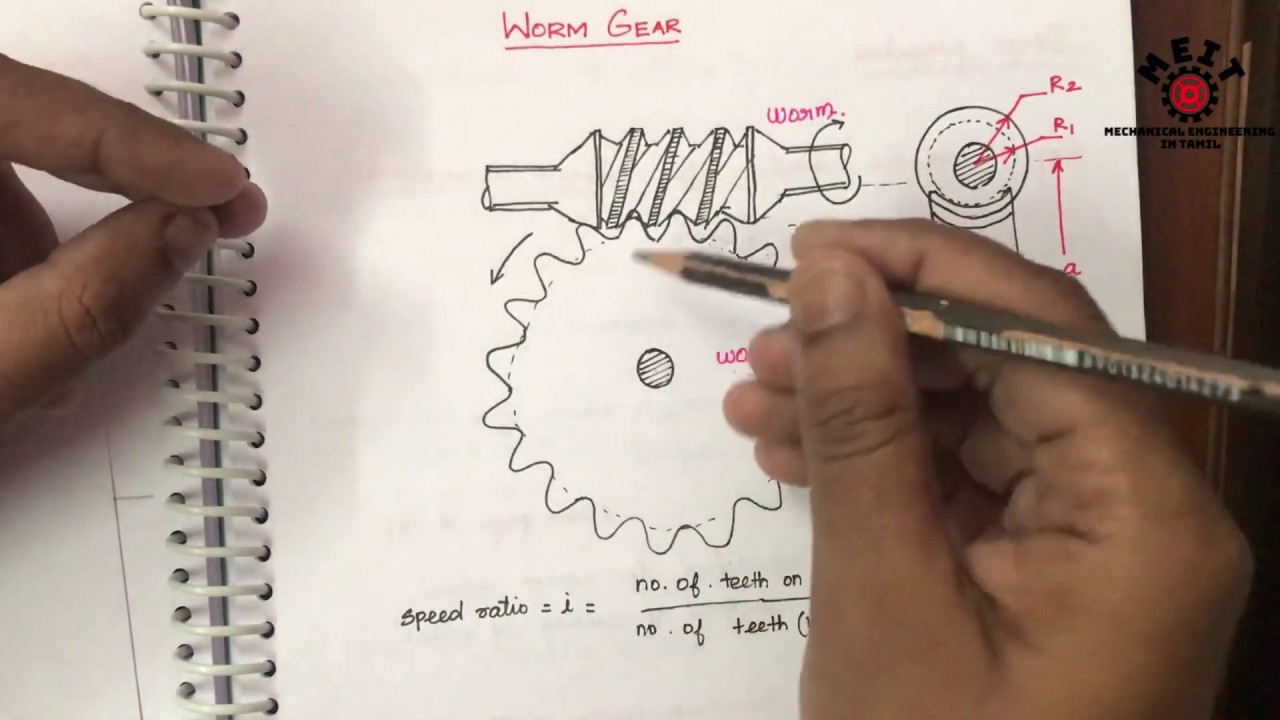
Worm tooth dimensions, such as addendum, dedendum, pressure angle, etc., follow the same standards as those for spur and helical gears.
